Ламинированные напольные покрытия в настоящее время широко распространены, их выбирают в бытовые помещения в качестве бюджетной альтернативы традиционным деревянным полам. В этой статье расскажем об истории появления ламината, его структуре, достоинствах и недостатках.
История развития ламината
Для начала определим, что именно стоит называть ламинатом. Говоря сухим технологическим языком, ламинированные напольные покрытия – отделочные материалы, представляющие собой древесноволокнистые плиты средней и высокой плотности, облицованные плёнками на основе термореактивных полимеров.
Впервые технологию ламинирования древесной плиты и использования её в качестве напольного покрытия предложили технологи компании Pergo в конце 70х годов прошлого столетия. Технология изготовления первых ламинированных покрытий была простой: декоративный слой пропитывался меламиновой смолой, нижняя часть доски производилась на основе фенольной смолы. Далее под воздействием высокого давления и температуры эти слои соединялись между собой, затем приклеивались на основу (ДСП плиту) при помощи термоактивного клея. Такая технология давала надёжное, прочное и износостойкое покрытие, однако требовала значительных затрат на производство и не могла обеспечить массовый выпуск продукции, поэтому не получила широкого распространения.
Прорыв в производстве ламината произошёл в 90х годах – в Германии была разработана технология прямого прессования (DPL). Она значительно ускорила и удешевила процесс выпуска ламината, так как производство стало осуществляться за одну технологическую операцию. В настоящее время по DPL технологии изготавливается более 90% ламинированных покрытий.
Следующим витком стало появление технологии непрерывного прессования (CPL), позволившей ещё сильнее снизить производственные затраты и, как следствие, стоимость продукции.
DPL и CPL технологии требуют более плотной и твёрдой основы, чем ДСП, поэтому в ламинате, изготовленном данными способами, используются основы из HDF или MDF плит.
Структура ламината
Современное ламинированное покрытие, вне зависимости от технологии производства, имеет практически одинаковый набор слоёв (кроме крафт-слоя, отсутствующего в технологии DPL).
-
Защитный слой – верхний слой, защищающий декор от истирания. Определяет устойчивость покрытия к механическому изнашиванию, защищает от образования пятен, влаги и воздействия химических веществ. Представляет из себя прозрачную целлюлозную бумагу (пергамин), пропитанную меламиновыми смолами, куда могут входить также частицы корунда (оксид алюминия). В процессе производства данный слой сплавляется с нижними слоями и становится прозрачным. Прочность верхнего слоя определяется количеством меламиновой смолы, используемой при пропитке, а от его толщины зависит износостойкость покрытия. Характеристики именно этого слоя влияют на износостойкость ламината.
-
Декоративный слой – изображение декора, обеспечивающий привлекательный вид покрытия. Выполняет исключительно визуальную функцию. Слой состоит из крафт-бумаги, пропитанной меламином, на которую нанесено изображение. Современный уровень развития печатных технологий позволяет воспроизвести на ламинате практически любые материалы – дерево, камень, металл, керамическую плитку и тд.
-
Основной слой – отвечает за общую толщину, прочность, коэффициент теплоизоляции. Представляет из себя спрессованную плиту из древесного волокна толщиной от 6 до 12 мм. Сама плита изготавливается из волокон хвойных (редко – лиственных пород), спрессованных под высоким давлением. В качестве связующих компонентов добавляются карбамидные и меламиновые смолы. Такие плиты не подвергаются гниению и не поражаются живыми организмами. Именно в основном слое в процессе изготовления ламината вырезаются замки. Плотность плиты влияет на прочность замкового соединения. Наиболее распространены древесноволокнистые плиты высокой плотности (HDF – High Density Fiberboard); однако некоторые производители используют плиту средней плотности (MDF - Medium Density Fiberboard).
-
Стабилизирующий слой – обеспечивает стабильность размеров покрытия, защищает от негативных внешних воздействий снизу. Стабилизирующий слой представляет собой один или несколько слоев крафт-бумаги из хвойных пород дерева, пропитанной меламином. В процессе изготовления он надежно спрессовывается с несущей плитой. У ламината бюджетного класса используется, как правило, один слой крафт-бумаги, а в покрытиях более высокого класса используется несколько слоев.
У некоторых производителей ламинированных покрытий, использующих технологию HPL и CPL, присутствует дополнительный слой из крафт-бумаги. Состоит из бумаги, изготовленной из хвойных пород древесины, пропитанной меламином. Обеспечивает дополнительную защиту покрытия от влаги, ударов и продавливания.
Повторяемость рисунка
Данное понятие означает количество досок, через которое встретится плашка с таким же рисунком. Повторяемость рисунка определяется в первую очередь технологией производства. Как правило, чем дороже ламинат, тем реже будут повторяться одинаковые доски покрытия.
Если привести статистику, то средний показатель повторяемости рисунка ламината примерно 1:20. У некоторых европейских производителей повторяемость рисунка достигает 1:60. У бюджетного ламината показатель менее 1:10, доски повторяются практически в каждой упаковке.
Плотность плиты
Древесноволокнистые плиты изготавливаются из мелких опилок, вырабатываемых из цельной древесины или отходов деревообрабатывающего производства. Опилки перемалываются, обрабатываются паром и подаются на тёрочную машину. Протёртое сырьё просушивается, перемешивается со смолами и затем прессуется.
Древесноволокнистые плиты по плотности разделяют на:
-
плиты низкой плотности – LDF (200-600 кг/м3)
-
средней плотности – MDF (600-800 кг/м3)
-
высокой плотности – HDF (от 800 кг/м3)
Замковое соединение ламината, изготовленного из MDF плиты, будет не особо прочным, так как высокую плотность имеют только верхние слои плиты толщиной около 1 мм, посередине плотность может быть вдвое меньше. Поэтому в характеристиках MDF плиты указываются границы плотности – в середине и на поверхности.
Для HDF плит показатель плотности одинаков по всей толщине, у ламината премиум-класса может достигать 1200 кг/м3. Такие показатели обеспечивают гарантию качественного и надёжного замкового соединения.
Технологии изготовления
Суть всех технологий изготовления ламината сводится к одной задаче: объединить все слои в единое целое. Вне зависимости от технологии процесс объединения слоёв производится под давлением и при высокой температуре. Из-за того, что защитный, декоративный и стабилизирующий слои имеют в своём составе меламиновые смолы, при нагревании они очень прочно скрепляются с основой – плитой, создавая единое покрытие.
В настоящее время используются 3 основные технологии изготовления ламинированных напольных покрытий:
-
HPL – раздельное прессование
-
DPL – прямое прессование
-
CPL – непрерывное прессование
Рассмотрим их подробнее.
Название технологии – сокращение от английского High Pressure Laminate (ламинат высокого давления). Особенность метода - поэтапное производство с применением высокотехнологичного оборудования. Процесс сложный и дорогостоящий, включает в себя несколько этапов горячего прессования под высоким давлением:
Этап 1. Прессуются защитный, декоративный и крафтовый слои бумаги в отдельной камере под очень высоким давлением (ок. 2,5 млн кг/м2) при температуре 140 °C.
Этап 2. Полученный HPL слой (толщиной около 0,6 мм) соединяется с несущей плитой и нижним стабилизирующим слоем.
Данная технология позволяет создавать покрытие с очень высокими прочностными характеристиками. Недостаток – высокая стоимость.
Технология DPL – прямое прессование
DPL – сокращение от Direct Pressure Laminate, ламинат прямого прессования. 90% всех ламинированных полов выпускается по данной технологии. Прямое прессование – по сути упрощение HPL технологии, где производство сведено к одной операции: прессованию всех слоёв одновременно при высокой температуре.
В процессе производства на плиту-основу накладывается декоративная бумага, покрывается защитным слоем, другая сторона основы покрывается стабилизирующим слоем из плотной бумаги. Затем все слои спрессовываются при температуре около 200 градусов Цельсия по давлением до 3000 кг/м2. Сцепление слоёв занимает менее минуты – этого достаточно для прочного скрепления. Благодаря сокращению времени, затраченного на производство продукции, удалось значительно снизить себестоимость покрытия.
Технология DPL требует высокой прочности от несущей плиты, поэтому на сегодняшний день на рынке практически не встречается ламинат, изготовленный из плиты средней плотности (MDF).
Технология CPL – непрерывное прессование
CPL – сокращение от Continue Pressure Laminate, ламинат непрерывного прессования. Технология близка к DPL: объединение слоёв производится за один этап, отличие заключается в использовании одного или нескольких крафт-слоёв под декоративным слоем. Это позволяет значительно увеличить прочность CPL ламината по сравнению с DPL.
CPL ламинат более устойчив к механическим воздействиям, чем ламинат DPL, но всё же менее прочный, чем ламинат высокого давления HPL. На данный момент всего около 10% ламинированных напольных покрытий изготавливаются по технологии непрерывного прессования.
Типы замков ламината
Все замковые системы у ламинированных полов можно разделить на 2 большие группы: Lock и Click. Эти замки различаются методом стыковки соседних плашек.
Замки Lock сейчас практически не встретить
Замок типа Lock является морально устаревшим, изготавливается лишь на старых производственных линиях. Соединяющий элемент выглядит как шип, оснащённый гребнем, входящим в паз на другой стороне панели. Сборка происходит в горизонтальной плоскости путём подбивания элементов. Данный тип замка сложно разобрать, не повредив, а профиль часто изнашивается со временем от постоянных нагрузок и трения.
Большинство современных ламинированных покрытий имеют замки типа Click, лишённые недостатков Lock-замков. Они имеют форму замыкающего шипа в виде плоского крюка, в пазах предусмотрены площадки для его вхождения. Такая конструкция надёжно удерживает панели, предотвращая появление щелей даже при высоких нагрузках.
Поколения замков ламината
Все замки ламинированных напольных покрытий условно делятся на 3 поколения:
1G. Замки типа Lock. В настоящее время практически не используются.
2G. В замках такого типа «шипы» располагаются по одной длинной и короткой стороне доски, по двум другим нарезаны «пазы». При сборке покрытия вначале надо собрать весь ряд (соединяя доски по торцевой стороне) а затем соединить собранный ряд с предыдущим по длинным сторонам.
5G. В данном типе замка по длинной стороне тип замыкания такой же, как у 2G, а для соединения по торцевой стороне присутствует специальная пластиковая вставка, облегчающая защёлкивание и делающая процесс сборки быстрым и простым. Покрытие собирается поштучно.
Замок Uniclic
В 1997 году технологами компании Unilin была разработана и запатентована технология соединения досок покрытия, получившая название Uniclic. Прочность замкового соединения Uniclic обеспечивается благодаря особому профилю замка, обеспечивающему натяжение после замыкания, которое сближает соединенные доски, гарантируя отсутствие щелей или промежутков между соседними плашками. Эта технология подходит для соединения досок как по длинной, так и по короткой стороне. В 2010 году корпорация UNILIN для защиты своих авторских прав на замковое соединение Uniclic составила программу L2C (Лицензия на замок). Этим лейблом снабжаются все ламинированные покрытия, изготовленные в Китае и официально применяющие технологию Uniclic в своей продукции.
Фаска у ламината
Фаска – скошенная под определённым углом к поверхности кромку. Угол скоса, как правило, составляет от 15 до 50 градусов. Впервые появилась на массивной паркетной доске, необходима была, чтобы скрыть неизбежный разрыв лакового покрытия.
Ламинат с фаской, кроме сходства с натуральным паркетом, решил проблему задирания кромок верхнего меламинового слоя при использовании покрытия, но при этом появилась проблема с влагостойкостью. На ламинате фаска формируется исключительно фрезерованием, при нём снимается верхний защитный слой и открывается доступ влаги в основную древесноволокнистую плиту.
У современных ламинированных напольных покрытий используется два вида защиты фаски:
-
Прокрашивание – поверхность фаски покрывается красящим составом с определёнными водозащитными свойствами. Минус – для качественной уборки покрытия требуется мощный пылесос, способный убрать всю пыль из щелей.
-
Ламинирование – поверхность фаски проклеивается крафт-бумагой. Это более дорогостоящий способ, применяется при формировании U-образных кромок, защищающий от воды, грязи и истирания.
Фаска на ламинате формируется исключительно при помощи фрезерования
Виды фаски на ламинате
Наиболее распространённые это V-образная и U-образная фаски, отличающиеся профилем фрезы, снимающей слой материала.
U-образная фаска своими мягкими, округлыми переходами между досками создаёт эффект «деревенского» пола. Чаще всего встречается V-образная фаска, формирующая треугольник с чёткими гранями острием вниз. В некоторых дизайнерских коллекциях ламината встречаются неравномерные фаски, создающие эффект неровности, присущий натуральному дереву.
Помимо этого, фаска может быть снята со всех 4х сторон доски (4U или 4V) или только по длинным её сторонам (2U или 2V), что создаёт так называемый эффект бесконечной доски, визуально удлиняющий помещение
На что влияет толщина ламината
Широко распространено мнение, что чем толще ламинат – тем лучше. Это утверждение истинно для паркетной доски и массивного паркета, качество ламинированного покрытия определяется в первую очередь плотностью древесноволокнистой плиты.
На рынке представлены ламинированные напольные покрытия толщиной от 6 до 12 мм:
-
6-7 мм считается бюджетным, в настоящее время практически не встречается
-
8-10 мм можно называть оптимальным выбором, поскольку такая толщина плиты обеспечивает возможность нарезания качественного и прочного замкового соединения.
-
свыше 12 мм исключительно маркетинговые продукты, серьёзного увеличения качественных характеристик не наблюдается, а стоимость существенно выше.
Однако стоит отметить, что при прочих равных характеристиках ламинат большей толщины будет обладать лучшими прочностными характеристиками.
Из чего складывается цена ламината?
Цена на ламинат определяется стоимостью основной плиты и верхнего слоя. С целью сокращения расходов, производители бюджетного ламината из Юго-Восточной Азии увеличивают содержание связующих компонентов в плите, чтобы обеспечить необходимую плотность. На выходе получается достаточно бюджетный продукт, но вызывающий много сомнений в безопасности покрытия.
Материалы, входящие в состав ламината ведущих европейских производителей абсолютно безопасны для здоровья человека. Это подтверждается различными международными сертификатами.
Также на стоимость покрытия оказывает влияние диаметр печатного вала, наносящего декор (к вопросу о повторяемости плашек). Чем реже повторяются доски покрытия, тем дороже оно стоит.
Не стоит забывать и о стоимости использования патентованных технологий.
Стандарты качества. Ассоциация EPLF
С 2000-х годов популярность ламинированных напольных покрытий стремительно стала расти, как и количество производителей. Это подтолкнуло европейских производителей ламината к созданию EPLF – ассоциации европейских производителей ламинированных напольных покрытий. На сегодняшний день в ассоциацию входят 18 производителей ламинированных напольных покрытий, 20 компаний-поставщиков и 10 спонсирующих организаций. В 2006 году с подачи EPLF был разработан европейский стандарт EN 13329:2006, призванный упорядочить технические характеристики ламината, приведя их к единой классификации по сфере использования. Так появились классы ламината.
Классы ламината
По интенсивности механического воздействия, которое способно выдерживать покрытие, любые покрытия разделяются на классы согласно ГОСТ 58898-2020.Классы ламината –это комплексный показатель, который присваивается покрытию по результатам ряда испытаний. В 2006 году появился европейский норматив EN 13329:2006, определяющий классы ламината, а в 2013 году вышел российский ГОСТ 32304-2013, являющийся переработанной версией европейского регламента.
Классы ламината по EN 13329:2006
По европейским нормативам ламинату присваивается класс на основании показателей:
-
класс истираемости,
-
класс ударной прочности,
-
устойчивость к образованию пятен,
-
устойчивость к прожигу сигаретой,
-
результат при имитированном смещении ножки мебели,
-
испытание роликами стула,
- набухание образца по толщине.
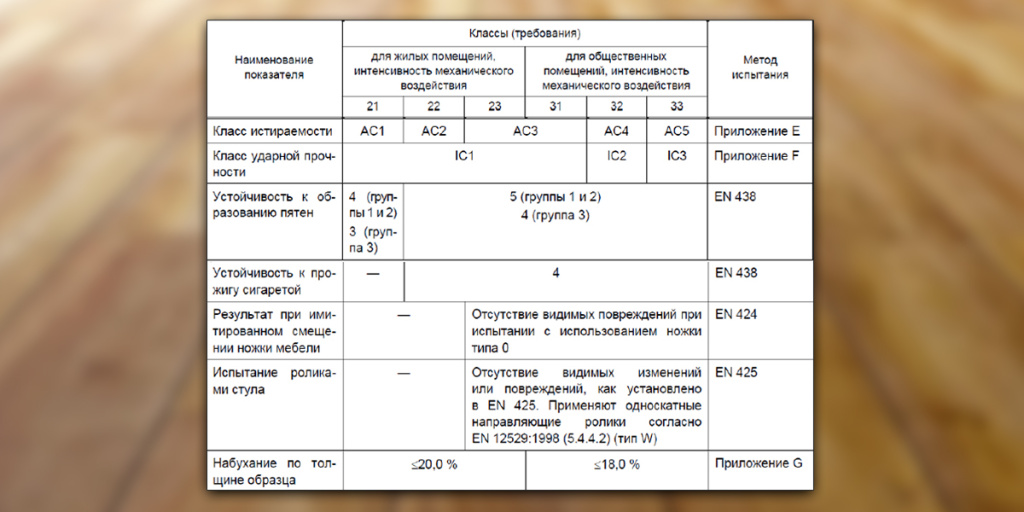
Классы ламината по ГОСТ 32304-2013
По российскому стандарту ламинированным напольным покрытиям присваивается класс нагрузки на основании следующих показателей:
-
Устойчивость покрытия к истиранию
-
Устойчивость к пятнообразованию
-
Сигаретостойкость
-
Разбухание по толщине на 24 часа
Укладка покрытия
Весь ламинат укладывается исключительно «плавающим», или свободнолежащим способом без приклеивания к основанию.
Подготовка к монтажу покрытия. Требования к основанию
Перед началом монтажа необходимо подготовить основание. Требования к нему не особенно отличаются от других напольных покрытий: оно должно быть ровным, твёрдым, чистым и сухим. Перепад ровности основания должен составлять не более 2 мм на погонный метр, проверяется при помощи строительного уровня.
Инструменты понадобятся простые – это ножовка, карандаш, подбивочный инструмент (например, брусок), клинышки.
Сопутствующие материалы
Дополнительно для укладки ламината потребуется подложка и гидроизолятор. В роли гидроизолятора выступает целлофановая плёнка толщиной не ниже 200 микрон, укладываемая внахлёст. Роль гидроизолятора – предотвращать возможное поступление влаги из основания пола. Многим кажется ненужным заморачиваться с укладкой плёнки – зачем, если есть подложка? Следует запомнить: подложка не является барьером, препятствующем прониканию влаги.
Основная роль подложки – снижение ударного шума. Без подложки звуки шагов или падающих предметов будут разноситься далеко – так называемый эффект барабана. Она не поможет выровнять основание, нет никакой необходимости в приобретении толстой подложки – это приведёт к продавливанию покрытия, размыканию или поломке замков у покрытия. Оптимальная толщина подложки составляет 2 мм. При выборе вида подложки стоит опираться на стоимость, но при этом учитывать, что вспененный полиэтилен, например, быстро истончается, а пробковая подложка со временем может начать крошиться.
Монтаж покрытия
Самые простые в сборке замки типа 5G, укладка 2G замков потребует наличие опыта и сноровки. Подробнее о них рассказывали выше.
Крайне важно оставлять расширительные зазоры вдоль стен, это связано с изменением геометрических размеров покрытия при перепаде влажности и температуры в помещении. Если этим пренебречь, это может привести к деформации замков ламината, материал станет «домиком».
Укладка без порожков в разных помещениях, разделённых дверным проёмом, невозможна. Что касается допустимой площади для свободной укладки, у каждого производителя имеется свой норматив.
Совместимость с тёплыми полами
Ламинат совместим со всеми видами систем «тёплый пол». При использовании не стоит забывать о предельно допустимой температуре нагрева основания – 28 градусов Цельсия. Также увеличение температуры нагрева должно происходить со скоростью не более 5 градусов в сутки. Это не прихоть производителей, данные требования прописаны в СНиП 41-01-2003. Несоблюдение требований и перегрев вредит не только внешнему виду покрытия, но и вашему здоровью.
Ламинат совместим со всеми видами тёплых полов.
Уход за ламинатом
Уход за ламинатом крайне простой и не требует специализированных средств. Можно использовать все современные моющие средства, за исключением хлорсодержащих средств и абразивов. При влажной уборке тряпка должна быть хорошо отжата.
Использование моющих пылесосов и паровых швабр на постоянной основе нежелательно, так как постоянное воздействие влаги (тем более горячего пара под давлением) может привести к попаданию влаги в стык между плашками и, как следствие, риску его разбухания.
Недостатки ламината
В заключение стоит отметить, что несмотря на декоративность покрытия, отличную износостойкость и лёгкость укладки, ламинат обладает и несколькими существенными недостатками.
Чувствительность к влаге – несмотря на усилия производителей, основной сферой применения ламината остаются «сухие» помещения.
Пожароопасность – класс пожарной опасности ламината, как правило, КМ5, что не позволяет использовать его в некоторых типах зданий. Да, на рынке существует ламинат с классом КМ2, однако такой параметр достигается применением большого количества огнестойких пропиток, что ставит под сомнение его экологичность.
Косвенное влияние на уничтожение лесов – неочевидный недостаток, однако цифры говорят сами за себя: для производства 1 м3 MDF или HDF плиты требуется 4 м3 древесины. Ежегодно в мире реализуется около 500 млн м2 ламината, выходит, что для производства такого объёма уходит около 20 млн м3 древесины – около 80 млн деревьев, растущих на площади, примерно равной площади Санкт-Петербурга.